Apr. 26, 2022
Working High Up: CC 3800-1 Erects Wind Turbine On The Gotthard Massif
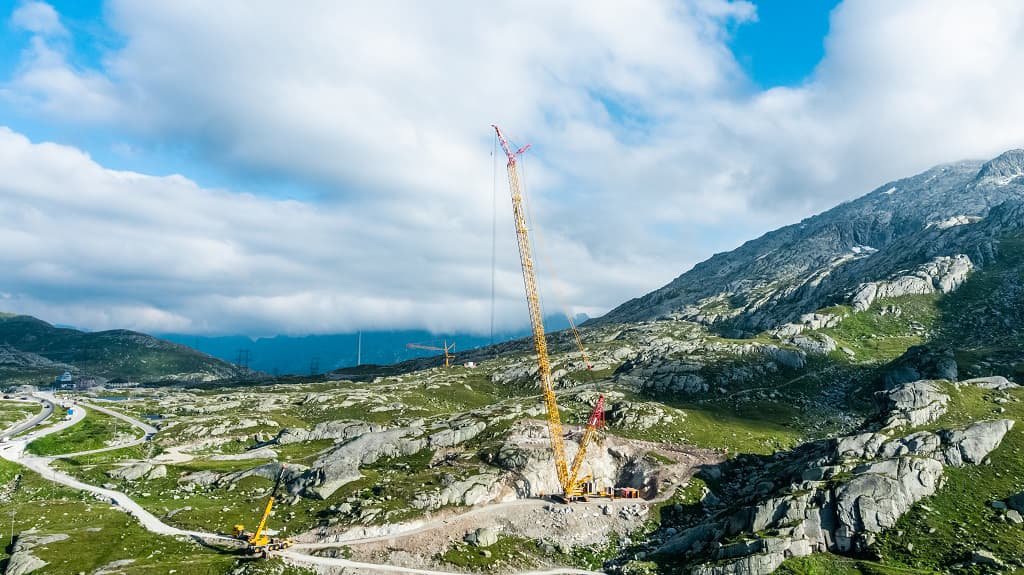
“Setting up a crawler crane in this kind of terrain really requires the use of specialists,” Manuel Widmer, who is in charge of large-scale projects at Toggenburger, says while explaining what the biggest challenge involved in the demanding project was. After all, the team faced a whole series of adversities at the St. Gotthard wind farm, at an altitude of over 2,000 meters: Not only was the work area extremely tight, but it was also about 20 meters lower than the foundation for the Enercon E 92 wind turbine. And since this was accompanied by the absence of a sufficiently large flat area, the 132-meter boom had to be installed “downhill” with a gradient of four degrees. Given these conditions, the company decided to play it safe, and accordingly brought Tadano CC specialist Willi Friesen on board to get assistance from the manufacturer while planning the whole thing.
The CC 3800-1 was actually somewhat oversized for the Enercon E 92 wind turbine, which was just under 100 meters tall – but the fact is that the site conditions also left Toggenburger with no other choice: On one hand, there was the relatively large distance of 32 meters between the crane setup area and the wind turbine foundation, which would require working with a correspondingly large radius. On the other, the setup area was located 18 meters below the tower foundation, meaning that this difference had to be added to the wind turbine’s actual height. Ultimately, however, using the large 650-tonne crane came with an advantage: “Thanks to the CC 3800 1’s extraordinary lifting capacity in an LH+LF3 configuration, even without the Superlift system, we were able to cost-effectively offer Enercon an additional crane for erecting towers at the wind farm,” reports Manuel Widmer
Unique boom setup conditions
But before getting to that point, Toggenburger’s planning expertise had to play a vital role. For starters, the team meticulously measured every single dimension at the setup area, including all obstacles and differences in altitude at the site. During this process, it turned out that putting together the boom as usual would not be possible due to an unavoidable downhill slope of 4°. In other words, there had to be a special plan for setting it up. During this planning phase, the team got Willi Friesen involved in order to get crucial assistance in the form of Tadano’s designated CC crane expert. “The downhill slope on rough and uneven terrain, combined with the tight space conditions, meant that the boom and LF had to be put together while suspended in the air,” the CC specialist explains. He also made sure to get an analysis indicating the main boom points that had to be undergirded so that the structure would not be overloaded. “Willi Friesen was an absolute godsend, and this type of flexible and expert support is something we truly appreciate about the Tadano team,” Manuel Widmer highlights.
Once at the site, there was yet another potential hindrance: The assist crane was only able to work at a large distance from the CC 3800 1, and the components had to be brought one by one from the temporary staging area. Not to mention, of course, that every time the truck drove to the setup area, it had to go through an extremely tight, steep, and winding access road, which was a challenge in and of itself. “We had to reduce the corresponding weights significantly, and that meant, for example, removing the winches and A-frame from the base crane and bringing them to the mountain separately,” Manuel Widmer reports. And since the setup area itself had very little space for temporarily setting down the crane components, everything had to be delivered just-in-time from the temporary staging area: “Getting the crane parts to the mountain really was a logistical challenge,” Manuel Widmer points out.
The standard by which cranes should be measured
Despite all the adversities, the Toggenburger team managed to set up the crane and have it ready to start lifting within the planned timeframe. “Part of the reason we were able to do that was the fact that the CC 3800 1 can be set up extremely quickly and efficiently in comparison to competing products. Needless to say, our team’s extensive experience also played a key role,” Manuel Widmer says with equal praise for both the crane and the team.
Thanks to the team’s thorough preparation, the lifts themselves were business as usual: With an LSL + LF_6; 120-m + 12-m boom configuration, the CC 3800 1 was able to safely lift all components with a 20° LF offset at a radius of 32 meters with very little Superlift counterweight (on the decoupled Split Tray). The heaviest load was the nacelle, which came in at a weight of 65 tonnes: “And yet the crane could have easily handled more than that,” crane operator Stefan Graf confidently says before going on to show just how much of a fan of his CC 3800-1 he is: “The CC 3800-1 is absolutely reliable, and it has a lifting capacity that is remarkably large for a 650-tonne crane – especially with the Boom Booster. I’ve been working with this crane since the end of 2015, and I really have to say that it’s the perfect machine! I honestly don’t know where you’d get something that stacks up to it. To put it another way, it’s the standard by which all other cranes should be measured as far as I’m concerned.” Not surprisingly, this means that Toggenburger uses its CC 3800-1 regularly. In Switzerland, the company uses the crane not only for wind turbine projects, but also for bridge and plant construction work. “And since everything’s a bit smaller here in Switzerland, everything is just perfect – especially with the Vario Superlift system,” Manuel Widmer says as he points out another one of the crane’s advantages.
CC 3800-1 erects wind turbine on the Gotthard Massif